Porosity in Welding: Identifying Common Issues and Implementing Ideal Practices for Avoidance
Porosity in welding is a prevalent issue that frequently goes undetected up until it creates significant issues with the integrity of welds. In this discussion, we will check out the key factors contributing to porosity formation, examine its detrimental impacts on weld performance, and review the ideal methods that can be embraced to minimize porosity occurrence in welding procedures.
Common Reasons For Porosity
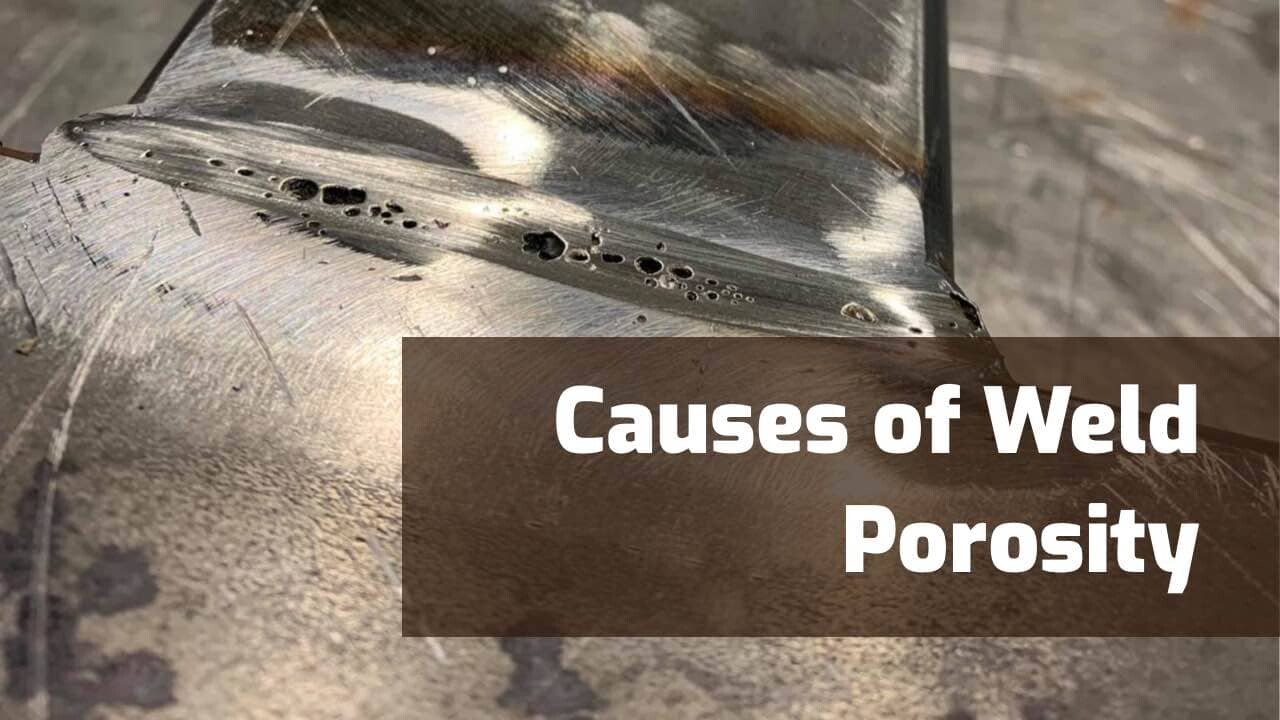
An additional frequent offender behind porosity is the presence of impurities on the surface of the base steel, such as oil, oil, or rust. When these impurities are not successfully eliminated before welding, they can vaporize and come to be entraped in the weld, triggering defects. Making use of unclean or damp filler materials can present impurities into the weld, adding to porosity problems. To mitigate these typical reasons for porosity, comprehensive cleaning of base metals, correct shielding gas selection, and adherence to ideal welding specifications are crucial practices in achieving top quality, porosity-free welds.
Effect of Porosity on Weld Top Quality

The presence of porosity in welding can considerably endanger the architectural integrity and mechanical properties of welded joints. Porosity creates spaces within the weld steel, compromising its overall toughness and load-bearing capacity.
Welds with high porosity degrees tend to show lower effect toughness and decreased ability to warp plastically before fracturing. Porosity can impede the weld's ability to properly transmit pressures, leading to premature weld failure and possible safety dangers in essential structures.
Ideal Practices for Porosity Avoidance
To improve the architectural stability and top quality of welded joints, what specific measures can be carried out to reduce the incident of porosity during the welding process? Porosity prevention in welding is crucial to ensure the stability and strength of the final weld. One efficient technique is correct cleaning of the base steel, eliminating any kind of contaminants such as rust, oil, paint, or dampness that can result in gas entrapment. Ensuring that the welding tools remains in excellent condition, with tidy consumables and proper gas circulation prices, can additionally substantially lower over at this website porosity. Furthermore, keeping a steady arc and managing the welding criteria, such as voltage, existing, and travel speed, helps develop a regular weld swimming pool that decreases the risk of gas entrapment. Making use of the proper welding technique for the details product being welded, such as changing the welding angle and gun position, can even more avoid porosity. Normal examination of welds and immediate remediation of any kind of problems recognized throughout the welding procedure are important methods to stop porosity and generate high-grade welds.
Significance of Appropriate Welding Strategies
Applying correct welding strategies is vital in guaranteeing the architectural integrity and quality of welded joints, building on the foundation of effective porosity avoidance procedures. Welding methods directly affect the general strength and resilience of the bonded structure. One key element of correct view it welding methods is maintaining the appropriate warm input. Too much warmth can bring about enhanced porosity because of the entrapment of gases in the weld pool. Alternatively, insufficient warmth may lead to incomplete combination, developing possible weak factors in the joint. Furthermore, utilizing the appropriate welding criteria, such as voltage, existing, and take a trip rate, is critical for accomplishing audio welds with very little porosity.
Moreover, the selection of welding process, whether it be MIG, TIG, or stick welding, need to align with the certain demands of the task to guarantee ideal outcomes. Appropriate cleaning and preparation of the base steel, as well as picking the best filler product, are likewise essential elements of efficient welding techniques. By sticking to these best techniques, welders can decrease the threat of porosity development and produce top quality, structurally audio welds.
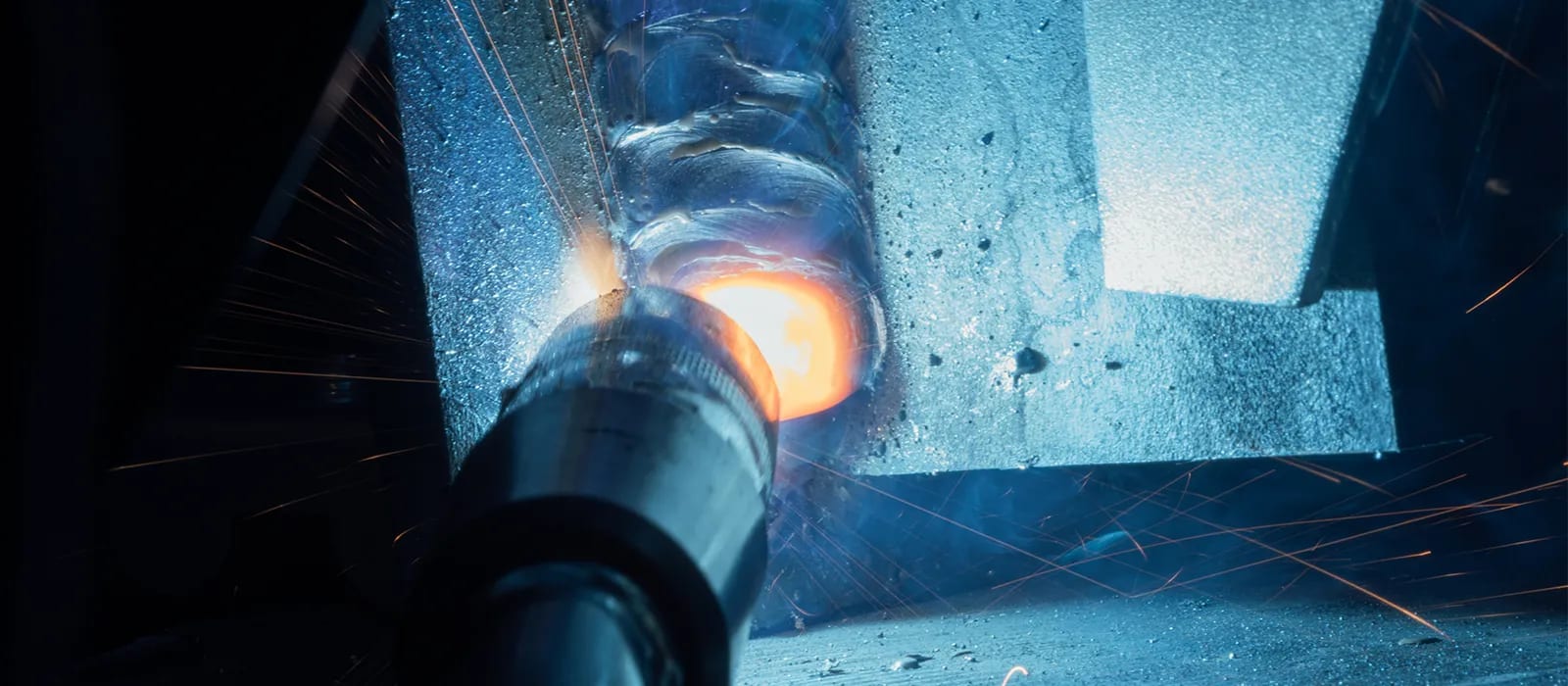
Examining and High Quality Control Steps
Quality control actions play an important duty in verifying the integrity and dependability of bonded joints. Testing procedures are important to identify and protect against porosity in welding, guaranteeing the stamina and toughness of the last product. Non-destructive screening approaches such as ultrasonic testing, radiographic testing, and aesthetic assessment are frequently utilized to recognize possible flaws like porosity. These strategies enable the evaluation of weld quality without endangering the honesty of the joint. What is Porosity.
Post-weld examinations, on the various other hand, evaluate the last weld for any kind of flaws, including porosity, and confirm that it fulfills specified requirements. Implementing an extensive quality control plan that consists of complete screening treatments and inspections is extremely important to lowering porosity issues and ensuring the overall top quality of bonded joints.
Conclusion
Finally, porosity in welding can be an usual problem that affects the high quality of welds. By recognizing recommended you read the common root causes of porosity and implementing best methods for prevention, such as correct welding strategies and screening actions, welders can make certain excellent quality and reliable welds. It is vital to prioritize prevention methods to minimize the event of porosity and preserve the honesty of welded structures.